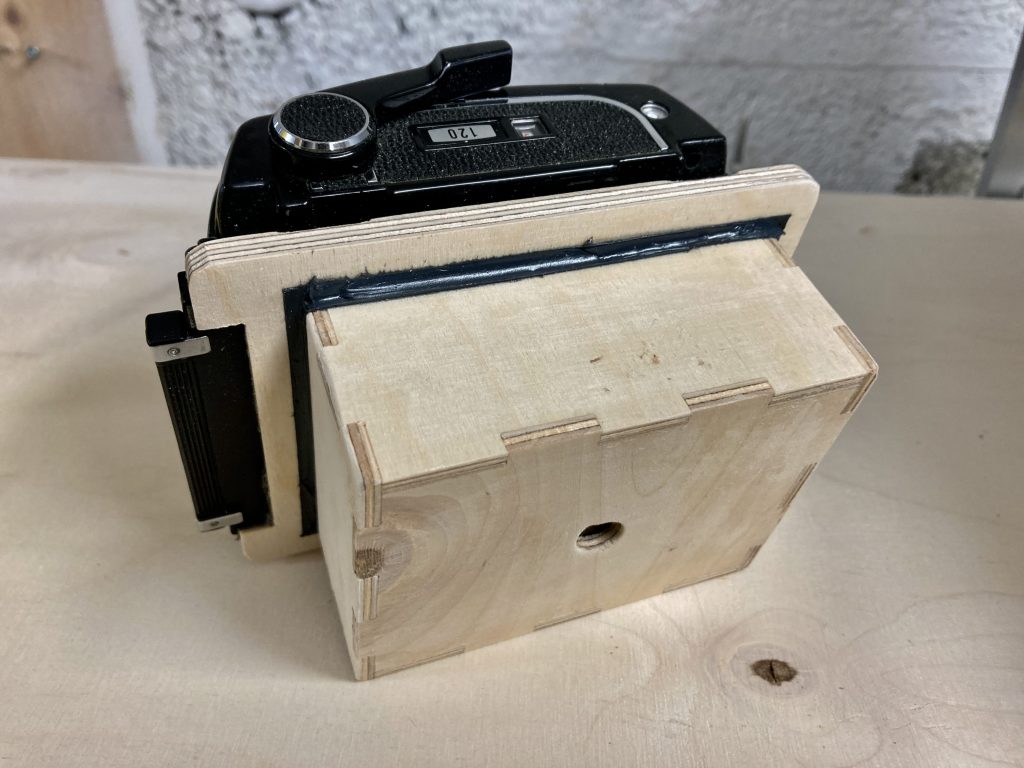
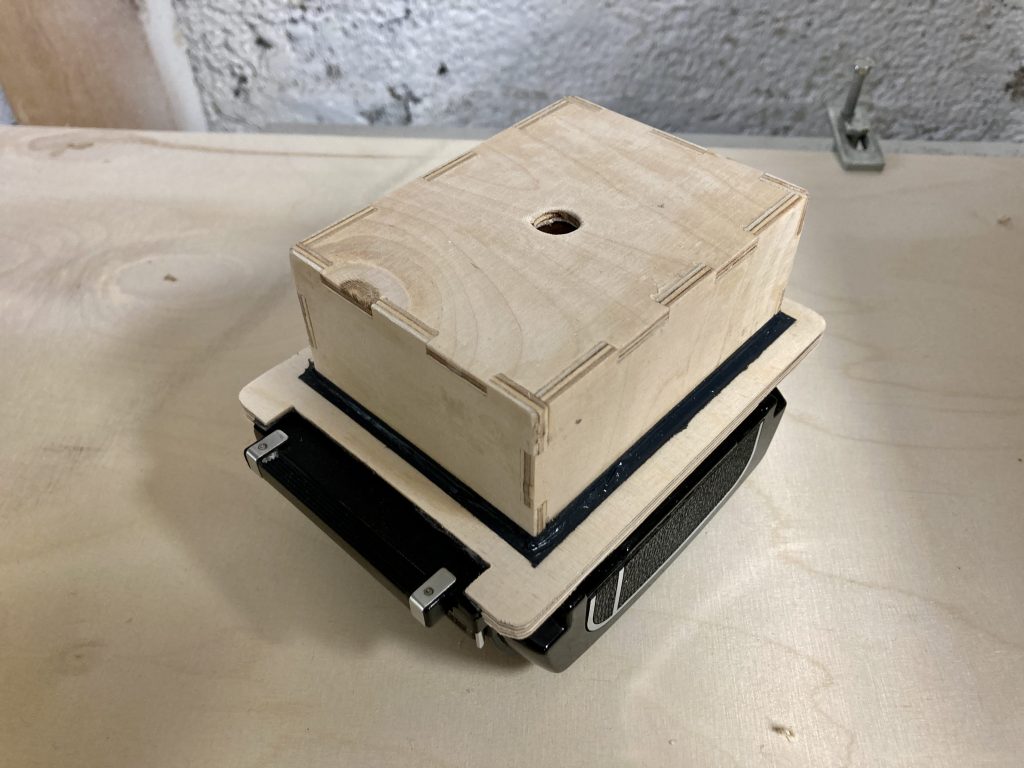

Here’s DXF design of Joerg’s original design. The holes in the file are 3.5mm but those are bit tight for 5mm tube that I used. I suggest 4.5mm – 5mm holes if you use 5mm silicone tube.
– Nema 17 steppers (Bipolar, 200 Steps, 42x42mm, 12V, 0.33A)
– A4988 Chinese stepper drivers
– 3S (12.6V) battery
– Arduino Pro Mini (5V, 16Mhz)
– Turnigy Evolution transmitter and TGY-iA6C Receiver
– MPU6050 gyro